The Centre for Advanced Materials (CAM) at Qatar University (QU) has successfully developed and implemented an innovative solar panel station with autonomous dry-cleaning technology.
This cutting-edge project is poised to be a cornerstone in renewable energy harvesting within the campus premises, notes an article by CAM director Prof Mohammad Refa’at Irshidat in the latest edition of QU Research Magazine.
The project tackles a major challenge hindering solar energy efficiency in Qatar - dust accumulation. A project led by Prof Irshidat and research staff members Dr Zubair Ahmad, section head of Module Development and Publication at QU Young Scientists Centre and Dr Kishor Sadasivuni, research assistant professor from CAM successfully installed autonomous dry cleaning systems for solar panels. The one ingenious technology uses a miniaturised wind turbine to run the self-sustainable dry-cleaning system while the second one utilises motorised brushes that automatically detect and remove dust, ensuring optimal performance.
The initiative began with a comprehensive study utilising wind turbine-based portable solar panel cleaning systems. Over a period of 30 days, various electrical parameters were measured to assess the performance of these panels. Real-time experiments at Al Duhail area confirmed a 5-8% efficiency improvement for solar panels equipped with the self-cleaning setup compared to those without any cleaning measures. The motor-based prototype consumes extremely low power due to the use of lightweight components and gives it an edge over other machines in the market.
The self-sustainable solar cleaning prototype features a wind turbine, gears assembly and a dry brush for efficient auto-cleaning of solar panels. Renewable wind energy is utilised to rotate the wind turbine attached to the top of the solar panel. The rotational motion of the wind turbine is converted into the linear motion of the cleaning brush via a gear and chain assembly. The gears were 3D printed using the fused deposition additive manufacturing method. The 3D printing gives control over the pitch of the groves in gear for precise rotation and reduces the weight of the attachment. The incorporation of 3D printed parts makes the design more susceptible to incorporate modifications and changes relatively based on the specific requirements of the end user.
The motor-based automated solar panel cleaning system operates based on input from the integrated dust detection sensor. Upon detecting dust accumulation on the solar panel, the cleaning process is activated and persists until the dust sensor feedback drops below the predefined threshold. Additionally, the cleaning apparatus is outfitted with sensors to restrict the movement of the cleaning brush within the confines of the solar panel frame. The designed cleaning system has extremely low power consumption and the cleaning methodology eliminates any type and mass of dust.
The developed prototypes can easily be installed on new solar panels or retrofitted with older ones. It is designed to work well for both flat and tilted solar panels, ensuring that nearly all angles are cleaned. The fully autonomous dry-cleaning system for solar panels is equally attractive and applicable for small, large and unattended installations in remote and dry areas where water is scarce. The developed prototypes are self-sufficient and work automatically. The dry-cleaning technology is non-abrasive, ensuring cleaning efficiency without affecting the solar panel glass surface. The system has been designed primarily to be simple, robust, lightweight, precise and credible.
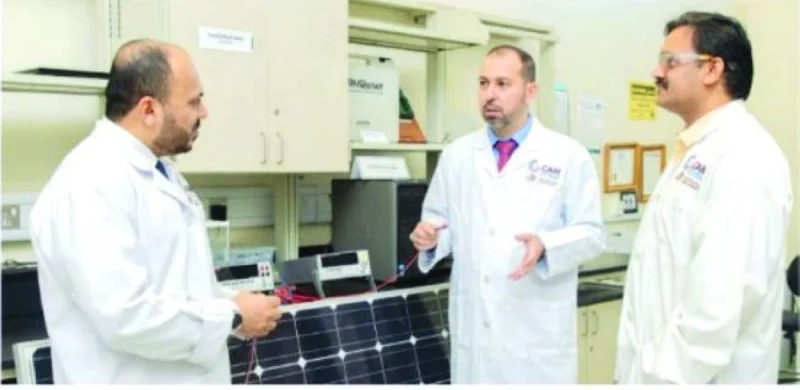
From left: Dr Zubair Ahmad, Prof Mohammad Irshidat and Dr Kishor Sadasivuni