Qatar's offshore oil fields in the Arabian Gulf are a key component of the region's energy landscape, contributing significantly to global oil and gas production. Drilling in these offshore environments, however, presents a host of unique challenges, especially in the top sections of wells where the risks of stuck pipes, blockages, and fluid losses can delay operations and drive up costs. In water depths ranging from 150 to 250 feet, drilling operations are further complicated by the delicate balance required between trajectory control and mud management to avoid catastrophic failures.
A team of engineers, led by Dmitry Kuravskiy, has recently proposed and implemented groundbreaking solutions that have transformed the efficiency and environmental footprint of top-section drilling in Qatar’s offshore oil fields. These innovations include enhanced control over well trajectory, optimized performance-driven strategies, and a deep focus on minimizing the environmental impact of drilling operations. Together, these advances have not only reduced drilling times by more than 70%, but have also contributed to significant cost savings and a reduction in carbon emissions—helping to set new benchmarks for offshore drilling worldwide.
The Complexity of Top-Section Drilling: Depths, Hole Sizes, and Engineering Challenges
The top-section drilling operations in Qatar's offshore fields occur at water depths between 150 to 250 feet, with well depths ranging from 500 to 3,000 feet. At these depths, precise control over the trajectory is crucial, particularly when drilling large-diameter holes of approximately two feet. For comparison, this is roughly the diameter of a medium-sized tree trunk, highlighting the sheer scale of the operation. The size of the hole and the variability of geological formations present unique challenges that demand constant monitoring and adjustment.
In offshore drilling, the top sections of wells are often the most unpredictable due to the complex interplay of soft seafloor formations, the risk of hitting obstacles, and the difficulty in maintaining wellbore stability. Traditional drilling methods, with frequent adjustments to the drill's trajectory, slow down operations and often lead to complications such as pack-offs—where cuttings and debris become lodged around the drill pipe, blocking progress and increasing the risk of stuck pipes.
The solution proposed by Dmitry Kuravskiy’s team was to take a more flexible approach, which allowed the drill to follow a broader range of acceptable paths within the formation, minimizing the need for constant directional corrections. This innovative solution meant that instead of making frequent adjustments, the drill was allowed to naturally find its path within predefined parameters, reducing non-productive time (NPT) and improving overall drilling speed.
Enhanced Trajectory Control: Navigating Depths with Precision
For wells ranging between 500 to 3,000 feet in depth, maintaining a consistent and accurate trajectory is paramount. The flexible drilling approach proposed by Kuravskiy’s team involved widening the operational "drilling window," allowing the drill to deviate slightly without the need for constant human intervention. This flexibility reduced the need for slide drilling (a slower, less efficient process) and increased the time spent in rotary mode, where the drill moves faster and more efficiently through the formation.
The team’s approach proved especially effective in reducing pack-off risks and tool failures. By allowing the drill to follow a natural trajectory, they significantly minimized the risk of stuck pipes—an issue that previously caused substantial delays. These improvements helped cut the time required to drill the top section of wells by more than half, significantly reducing the time from 6 days to as little as 2 days in some cases.
The implications of this are clear: faster drilling means lower operational costs and less time spent on-site, which in turn reduces the environmental footprint of the operation. By reducing the number of rig days required per well, Kuravskiy’s team not only improved the economic efficiency of the project but also laid the groundwork for a more sustainable approach to offshore drilling.
Real-Time Monitoring: Keeping the Operation on Track
The success of these innovations hinged on the team’s ability to monitor and adjust drilling parameters in real-time. With well depths reaching up to 3,000 feet, it was essential to have immediate feedback on the drill’s performance. Advanced sensors were placed along the drill string, providing real-time data on key factors such as weight on bit (WOB), rotational speed, and deviation from the intended well path. This allowed the team to make quick adjustments, preventing potential issues before they became costly setbacks.
This real-time monitoring system not only ensured that the drill stayed on course but also improved operational confidence. With constant data at their disposal, Kuravskiy’s team was able to push performance limits, drilling faster without increasing the risk of tool failure or equipment damage. This proactive approach to managing the drill’s trajectory and performance was a major contributor to the team’s ability to reduce overall drilling times by more than 50%.
Mud Management: Built on Previous Advances
While Kuravskiy’s team led the charge in improving trajectory control and real-time monitoring, the innovations in mud management were built on earlier contributions by peers in the field. The effective use of mud systems is vital in any drilling operation, particularly in offshore environments where blockages caused by poor mud circulation can halt progress and significantly delay operations.
Previous advancements by peers had introduced more effective timing of mud circulation and the use of sweeps to keep the well clear of debris. These innovations helped to stabilize the wellbore and prevent blockages, particularly in the top sections where the formation can be more unpredictable. Kuravskiy’s team capitalized on these innovations, integrating them into their broader drilling strategy to ensure that the wellbore remained clean and stable throughout the drilling process.
By using these mud management techniques in conjunction with their flexible drilling approach, the team was able to maintain the integrity of the wellbore, ensuring smoother and faster drilling operations. This combination of innovations led to a 75% reduction in non-productive time in the top section of wells, further enhancing the overall efficiency of the project.
Performance-Driven Strategy: Optimizing Every Step
One of the key innovations proposed by Dmitry Kuravskiy’s team was the introduction of a performance-driven strategy aimed at optimizing every step of the drilling process. By closely monitoring each phase of the operation in real-time, the team was able to quickly identify inefficiencies and make immediate adjustments to improve performance. This strategy was particularly effective in reducing connection times—the time spent changing tools or moving the drill—by more than 73%.
For comparison, this is akin to tuning a racing car’s pit stops. Just as in motorsports, where time lost in the pits can mean the difference between victory and defeat, in offshore drilling, every minute spent on non-drilling activities adds to the overall project cost. By optimizing these non-drilling phases, Kuravskiy’s team was able to save more than 12 days of operational time across multiple wells, resulting in significant cost savings and improved project timelines.
Environmental Impact: A Greener Approach to Offshore Drilling
Beyond the technical and operational benefits, the solutions proposed by Dmitry Kuravskiy’s team also had a substantial impact on the environmental sustainability of the drilling operations. By reducing drilling times by more than 70%, the team was able to save over 100 rig days per year. This decrease in rig days had a direct effect on the project’s carbon footprint, particularly in terms of fuel consumption and CO2 emissions.
Offshore rigs rely on diesel generators, and each day of operation consumes around 17,923 liters of fuel, resulting in approximately 48 tons of CO2 emissions per day. By reducing the number of rig days, Kuravskiy’s team prevented the emission of over 4,800 tons of CO2 annually —equivalent to the work of more than 796,922 trees or the sequestration capacity of a forest over 754 million square feet (about 27,437 acres) in size.
This reduction in emissions represents a significant step forward for the oil and gas industry, demonstrating that it is possible to increase efficiency while also reducing environmental impact. By improving operational performance and minimizing non-productive time, the team not only achieved substantial cost savings but also contributed to a more sustainable approach to offshore energy production.
A Blueprint for Future Success
The innovations proposed by Dmitry Kuravskiy and his team have set a new standard for offshore drilling in Qatar’s oil fields. By focusing on key challenges such as trajectory control, real-time monitoring, and overall process efficiency, the team has redefined what is possible in top-section drilling. Their solutions have not only shortened well delivery times but have also significantly reduced the environmental impact of drilling operations.
As the global oil and gas industry continues to face increasingly complex challenges, the strategies and technologies developed by Kuravskiy’s team offer a roadmap for achieving higher efficiency, lower costs, and a reduced carbon footprint. This transformation is not just about improving technical performance; it’s about setting new benchmarks in sustainability and paving the way for a more environmentally responsible future in offshore energy production.
Qatar
Revolutionizing offshore drilling in Qatar: Precision, performance, and environmental impact in top-section drilling
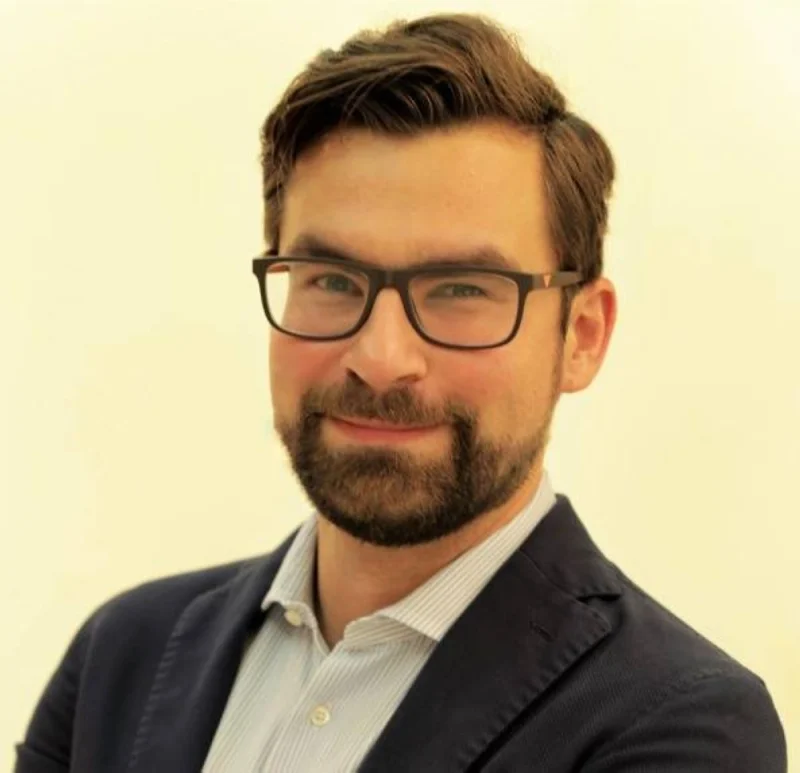