The heart of the project is an old shipping container, which three young Dutch architects converted to a 3D printer, the “Kamer-Maker” or “room-builder.” It has already produced stairs, walls, and parts of the façade, writes Annette Birschel
The enormous nozzle turns slowly, spraying out a millimetre-thin synthetic material which looks like ridiculously long spaghetti.
“That’s going to be a column,” says Nathalie Swords. The 25-year-old German architecture student is sitting on a camping stool and pauses now and then to type something into her laptop. “It’ll be 1.6 metres high. That’ll take eight hours.”
Swords is completing an internship at what is possibly the world’s most exciting construction site, in Amsterdam. In the borough of Noord, a canal-side house with four storeys, 13 rooms and the stepped gables typical of the Dutch city is being built — or rather, printed.
The scene is nothing like that of a typical building site. Neither cranes nor bulldozers trundle around the site, which is just behind Amsterdam’s futuristic film museum. Instead of the chug of cement mixers, there is the sound of seagulls screeching overhead and the quiet hum of the printer.
The heart of the project is an old shipping container, which three young Dutch architects converted to a 3D printer, the “Kamer-Maker” or “room-builder.”
It is 3 metres high and around 2 metres by 2 metres wide. It has already produced stairs, walls, and parts of the facade. Outwardly, one sees only the smooth surfaces. Inside, the elements are not solid, but have a honeycomb-type structure.
And now everything is ready to assemble — no bricklayers required.
“It’s like Lego for grown-ups,” laughs Hedwig Heinsman. The 34-year-old belongs to the trio from the Dutch architecture firm Dus which designed the canal house: narrow, tall and highly ornate gables, just like its 400-year-old predecessors, but without the red and white bricks.
The room-builder is fed with small white balls of organic matter.
“It’s made of 80-per-cent vegetable oil,” says Heinsman. It is heated up, fed through the nozzles and, like ink in a normal printer, sprayed onto the surface area. As soon as one layer is firm, the next is printed, millimetre by millimetre.
The German chemicals and glues corporation Henkel is a partner in the project and is developing the building material, for example from linseed. “Now and then we get a new sack with different balls to try,” says Heinsman.
Of course, the relatively light walls and the roof have to be able to withstand the blustery Amsterdam weather. Dutch firm Heijmans is developing the construction methods. For example, the hollow spaces between the individual parts could be filled with a concrete foam.
“3D technology is revolutionising the whole construction,” says Heinsman confidently. Anybody can be their own architect, she says, and design facades or rooms on the computer. “We just design the building’s DNA.”
The 3D house is also aimed at making architecture more affordable. It could also be used in disaster areas, say the Dus architects. Instead of having to transport expensive building materials, all that would be needed would be to set up a couple of the enormous printers and print accommodation from materials at hand.
Everything is possible, they say, from villas built out of old bottles to schools built from potato peelings. A builders’ hut on the site contains an exhibition on the building materials of the future, showing for example a tea service made of potato peelings.
That took even US President Barack Obama’s breath away, says Heinsman. On a visit earlier this year, he said “Wow!”
Amsterdam’s Dus architects are pioneers, even if they have lost the race to construct the world’s first printed house — China is reportedly already printing 10 bungalows a day.
“For us it’s not about the product but the process,” says Heinsman.
Those are no empty words — businesses, universities, city planners and Amsterdam’s citizens are also contributing to the project.
The production of the 3D-print canal house is continuing apace. A second giant printer has been set up, capable of printing parts up to 5 metres long. Soon the first sections will be put together on the banks of the IJ lake. Right opposite the traditional Amsterdam canal houses which inspired it.
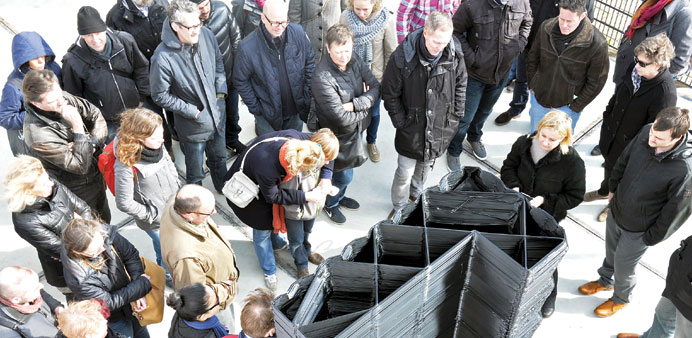
FIGURING OUT THE FANTASTIC: A guide explains to a group of visitors how honeycomb-style cells fill the centres of the printed elements making up a new